Mastering Injection Plastic Mold: A Comprehensive Guide for Metal Fabricators
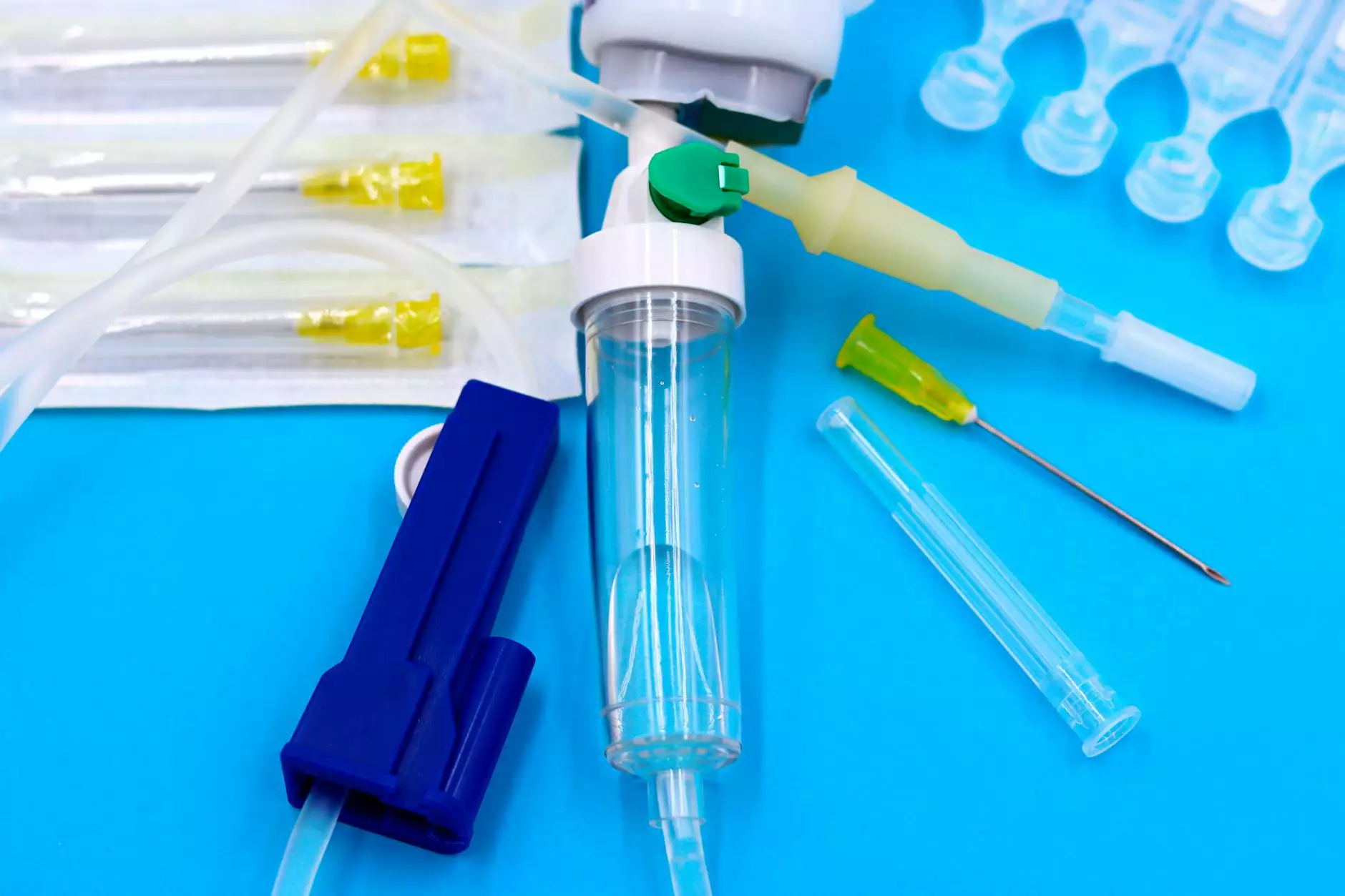
The world of metal fabrication is continually evolving, influenced by advancements in technology and design methodologies. One area that has gained significant traction is the use of injection plastic mold technology. This article will delve into the nuances of injection molding, its applications, benefits, and how businesses like deepmould.net can leverage this process for success in the competitive landscape of metal fabricators.
Understanding Injection Plastic Molding
Injection molding is a manufacturing process for producing parts by injecting molten material into a mold. The process can be applied to various materials, but plastic is among the most commonly used. In a typical injection molding cycle, several steps are performed to create high-quality components:
- Material Preparation: The plastic pellets are fed into a hopper and melted under heat and pressure.
- Molding: The molten plastic is injected into a mold cavity, where it cools and solidifies into the desired shape.
- Ejection: Once cooled, the mold opens, and the finished part is ejected.
- Post-Processing: Additional finishing processes may be applied, such as trimming, painting, or assembling.
The Importance of Injection Plastic Mold in Metal Fabrication
The integration of injection plastic mold technology into metal fabrication offers numerous advantages. It allows for the mass production of intricate designs that are often too complex or expensive to create through traditional methods. Below are several key reasons why this technology is essential:
- Cost Effectiveness: Once the mold is created, the cost per unit decreases significantly with large production runs.
- Design Flexibility: Injection molds can be intricately designed to produce highly detailed and complex shapes.
- Material Efficiency: Minimal waste is produced during the injection process, leading to a more sustainable practice.
- Consistency and Quality: Each part produced from a mold is almost identical, ensuring high-quality outputs for consumers.
Types of Injection Molding Processes
There are various types of injection molding processes used in the industry. Understanding these can help businesses select the right one for their production needs:
1. Standard Injection Molding
This is the most common method used, where plastic is heated to a molten state and injected into a mold.
2. Blow Molding
Used for hollow parts. The air is blown into the mold to shape the plastic into a desired hollow form.
3. Rotational Molding
This method involves heating plastic in a mold that is rotated to distribute the material evenly across the mold surface.
4. Insert Molding
Incorporates metal or other materials into plastic parts for added strength and functionality.
5. 3D Printing and Injection Molding Hybrid
An innovative approach combining additive manufacturing with traditional injection molding, allowing rapid prototyping and custom designs.
Applications of Injection Plastic Mold
The applications of injection plastic mold are vast and span several industries, including:
1. Automotive Industry
Parts like dashboards, door panels, and various interior components are often produced using injection molding.
2. Consumer Electronics
The casing and internal components of devices like smartphones and tablets utilize injection molding for precision and durability.
3. Medical Devices
Injection molding is critical for producing components that meet stringent hygiene and safety standards.
4. Packaging
From bottles to containers, the packaging sector relies heavily on injection molding for both functionality and aesthetic appeal.
5. Household Products
Items like toys, storage containers, and kitchen utensils are commonly made using injection molding techniques.
Benefits of Adopting Injection Plastic Mold Technology
Businesses that embrace injection plastic mold technology can unlock numerous benefits. Here are several compelling reasons to consider:
- Rapid Production: Parts can be produced quickly, allowing companies to meet demand more efficiently.
- Labor Efficiency: The process requires fewer operators than traditional methods, reducing labor costs.
- Reduced Lead Times: With advanced design and prototyping technologies, product development cycles are significantly shortened.
- Enhanced Customization: Tailoring products to meet specific customer needs becomes easier with injection molding.
- Improved Product Design: Freedom in design enables manufacturers to innovate and differentiate their products.
Challenges in Injection Molding and Solutions
While there are substantial benefits, businesses must also navigate several challenges associated with injection plastic mold processes:
1. High Initial Costs
The design and manufacturing of molds can be expensive. However, this can be mitigated through:
- Careful planning and design.
- Utilizing high-quality materials to ensure mold longevity.
- Investment in advanced manufacturing technologies like 3D printing for quicker and cheaper prototyping.
2. Material Limitations
Not all plastics can be used in injection molding. Working closely with suppliers and understanding material properties can lead to better material selection.
3. Waste Management
Although injection molding generally produces less waste, scrap is still an issue. It can be managed by:
- Implementing recycling protocols.
- Optimizing production processes to minimize flaws and defects.
Future Trends in Injection Molding
The field of injection molding is continuously evolving. Key trends that are shaping its future include:
1. Sustainability
A growing emphasis on eco-friendly practices is leading to increased use of biodegradable plastics and energy-efficient manufacturing processes.
2. Smart Manufacturing
Integration of IoT devices allows for real-time monitoring of production processes, ensuring higher efficiency and reduced downtime.
3. 3D Printing Innovations
The hybridization of 3D printing and injection molding is set to revolutionize manufacturing, enabling rapid prototyping and customized production runs.
4. Advanced Materials
Research into advanced composites and new polymers will enable the production of stronger, lighter, and more durable products.
Conclusion: The Future of Injection Plastic Mold in Metal Fabrication
In conclusion, the injection plastic mold technology offers a plethora of opportunities for metal fabricators. By embracing the advantages and navigating the challenges, businesses like deepmould.net can remain competitive in a rapidly changing industry. The combination of innovation, sustainability, and advanced manufacturing techniques will undoubtedly lead to a prosperous future for those who master the art of injection molding.
As more businesses discover the capabilities and benefits of injection molding, the potential for growth in the metal fabrication sector is immense. By investing in this technology and adopting best practices, companies can ensure they not only keep pace but thrive in the marketplace.