Unlocking the Potential of Die Casting Parts Factories
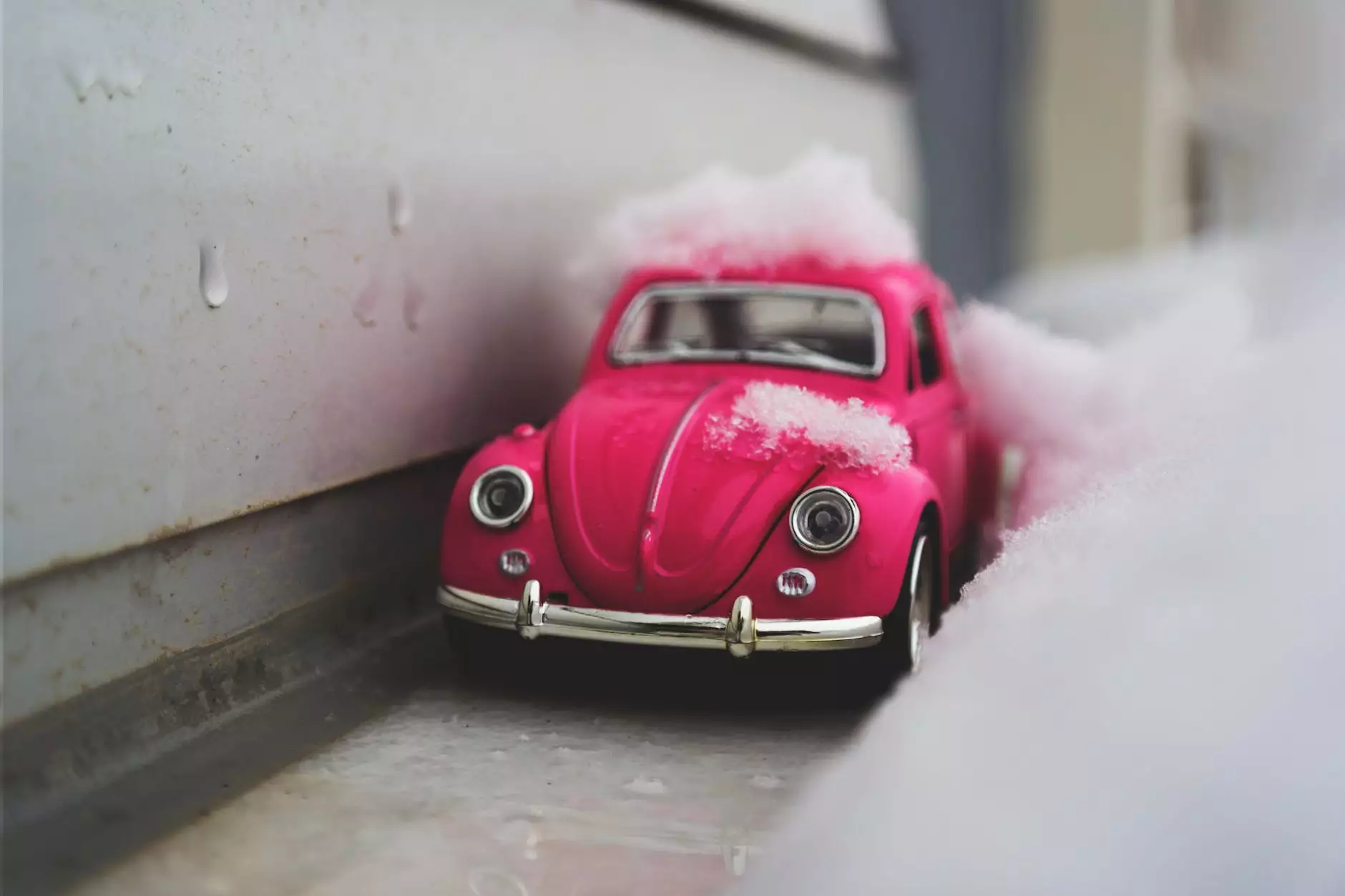
Die casting parts factories play a crucial role in modern manufacturing, providing essential components for various industries. With advancements in technology and techniques, these facilities are capable of producing high-quality, precise components that meet diverse industry demands. Whether you are in the automotive sector, electronics, or consumer goods, understanding the intricacies of die casting can significantly benefit your business.
What is Die Casting?
Die casting is a manufacturing process that involves forcing molten metal into a mold cavity to create parts with excellent dimensional accuracy and surface finish. This method is particularly suited for producing large volumes of parts with intricate shapes, significantly reducing the amount of machining needed while ensuring a smooth surface finish.
Types of Die Casting Processes
- High-Pressure Die Casting: This is the most common process where molten metal is injected at high pressure into a mold. It’s ideal for producing complex shapes and fine surface details.
- Low-Pressure Die Casting: In this method, metal is poured from a melt furnace into a mold under low pressure. It is used for larger and more massive parts.
- Gravity Die Casting: This traditional technique involves pouring molten metal into a mold utilizing gravity. It is typically used for producing simpler shapes.
The Role of Die Casting Parts Factories in Metal Fabrication
Die casting parts factories are instrumental in the metal fabrication industry. They allow for high-volume production of quality parts with reduced waste and lower production costs. The following points highlight their significance:
- Cost Efficiency: By utilizing efficient processes, die casting reduces material waste and labor costs.
- Precision and Accuracy: Advanced die casting technology ensures that parts are produced within tight tolerances, allowing for a perfect fit and function in assemblies.
- Complex Shapes: The ability to create intricate designs directly from a die minimizes the need for additional machining processes.
- Material Variety: Die casting can be employed with various materials, primarily aluminum, zinc, and magnesium alloys, providing options for different applications.
Innovations in Die Casting Technology
As the industry evolves, so does the technology that drives it. Modern die casting factories are continuously adopting new innovations that enhance productivity and quality. Some noteworthy advancements include:
Robotic Automation
Robotic automation in die casting has revolutionized the production line. Robots are used for tasks such as:
- Material Handling: Robots assist in moving materials to and from machines, minimizing human error and improving safety.
- Quality Control: Automated systems can quickly detect defects in parts, ensuring that only quality products reach the end client.
Advanced Mold Design
Employing advanced mold design technologies such as computer-aided design (CAD) and simulation software allows for more efficient mold development, reducing lead times and costs. Additionally, innovative cooling techniques can improve cycle times and part integrity, resulting in better final products.
Sustainability Practices
With a growing emphasis on sustainability, die casting parts factories are implementing eco-friendly practices. This includes:
- Material Recovery: Collecting and reusing scrap metal significantly reduces waste.
- Energy Efficiency: Upgrading equipment and utilizing renewable energy sources lowers the carbon footprint of manufacturing processes.
Choosing the Right Die Casting Parts Factory
Selecting a die casting parts factory for your manufacturing needs can be a daunting task. Here are key factors to consider when making this important decision:
Experience and Expertise
Look for a factory with a proven track record in die casting. A company with extensive experience understands the unique challenges and requirements of various industries, providing you with the best solutions tailored to your needs.
Quality Assurance Processes
The quality of the parts produced should be a top priority. Ensure that the factory utilizes rigorous quality assurance processes, including
- Regular Inspections: Routine checks during production to ensure compliance with standards.
- Testing Procedures: Implementing tests to verify the structural integrity and performance of parts.
Technological Capabilities
Inquire about the technology and equipment used in their processes. A state-of-the-art facility will offer better manufacturing capabilities, enhanced efficiencies, and superior product quality.
Customer Service and Support
Effective communication and support are crucial for a successful partnership. Choose a factory that offers:
- Responsive Communication: Quick and thorough responses to inquiries.
- Technical Support: Assistance with design or production issues.
Applications of Die Casting Parts
Die casting parts are widely utilized across multiple industries. Below are some areas where die casting makes a significant impact:
Automotive Industry
The automotive sector heavily relies on die casting for components such as:
- Engine Blocks: Complex shapes that require precision are best suited for die casting.
- Transmission Housings: Having lightweight but durable components is essential in automotive design.
Electronics
In electronics, die casting is used for:
- Heat Sinks: Efficiently dissipating heat in electronic devices is critical for performance and longevity.
- Chassis and Housings: Providing structure and protection for sensitive electronic components.
Consumer Products
Many everyday items also benefit from die casting, such as:
- Household Appliances: Components like frames and casings that require strength and aesthetics.
- Gardening Tools: Durable and functional products made using die casting techniques.
Conclusion: The Future of Die Casting in Metal Fabrication
The future of die casting parts factories is promising with continuous advancements in technology and an increasing demand for quality components. As businesses seek to optimize production processes and embrace sustainability, die casting remains a pivotal manufacturing method. Companies like deepmould.net exemplify excellence in metal fabrication, proving that with innovation, expertise, and a customer-focused approach, the industry can thrive.
By investing in a reliable die casting parts factory, businesses can ensure the delivery of high-quality products that meet or exceed industry standards, positioning themselves for success in an increasingly competitive market.