Understanding Injection Plastic Mold: Innovating the Future of Manufacturing
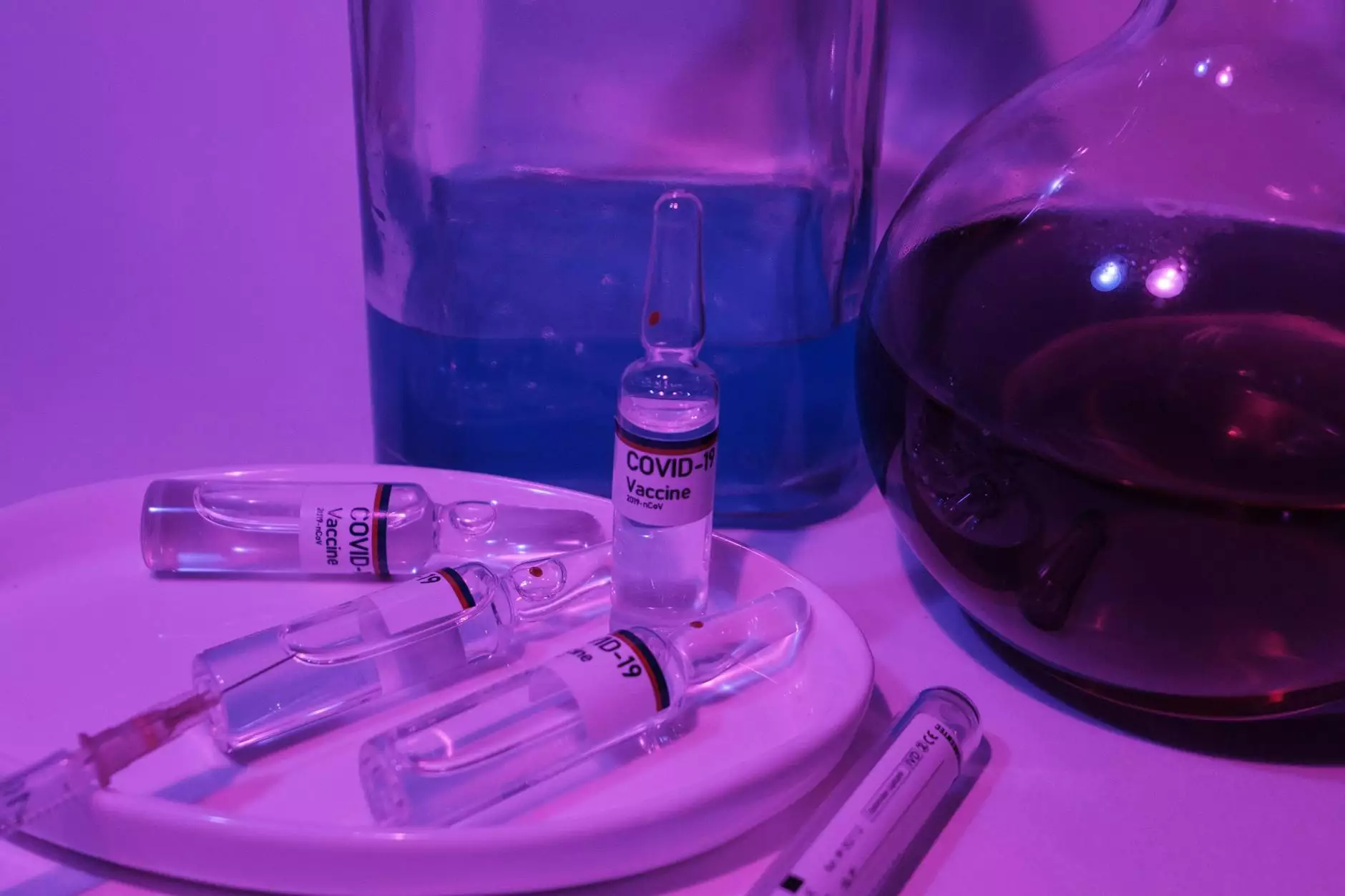
Injection plastic mold technology plays an indispensable role in the manufacturing industry, enabling businesses to produce complex plastic parts efficiently and cost-effectively. This article dives deep into the intricacies of injection plastic molds, exploring their significance, applications, and innovations that drive this vibrant sector forward.
What is Injection Plastic Molding?
Injection molding is a manufacturing process used for producing parts by injecting molten material into a mold. It is one of the most widely used manufacturing techniques for plastics, enabling high-volume production with exceptional precision.
The Process Explained
- Material Selection: The process starts with selecting a suitable plastic resin, commonly thermoplastics or thermosetting plastics.
- Melting: The plastic resin is fed into a heated barrel where it is melted to a liquid state.
- Injection: The molten plastic is then injected into a mold under high pressure.
- Cooling and Solidification: Once the mold is filled, the plastic cools and solidifies into the desired shape.
- Demolding: Finally, the mold is opened, and the finished part is ejected.
Advantages of Injection Plastic Molding
Injection molding offers numerous advantages that make it a preferred choice for manufacturers worldwide:
- High Efficiency: Once the mold is created, producing each part takes only seconds, translating to high productivity.
- Complex Shapes: Injection molding allows the creation of complex shapes and designs that would be challenging to produce with other methods.
- Material Variety: A broad range of materials can be used, including various plastics and composites.
- Minimal Waste: Since excess material can be reused, this method is more sustainable and cost-effective.
- Consistency and Precision: Each injection produces parts with tight tolerances and uniform quality.
Applications of Injection Plastic Molding
The versatility of injection plastic molds allows them to be used across various industries, including:
1. Automotive Industry
Injection molded parts are essential in the automotive sector, used for everything from dashboards to bumpers, providing necessary strength and durability while reducing weight.
2. Consumer Electronics
From casings for smartphones to internal components in laptops, precision-molded parts are found in a multitude of electronic devices, ensuring functionality and aesthetics.
3. Medical Devices
Injection molding is critical in producing medical devices and components, providing sterile, precise, and reliable parts that meet stringent regulatory standards.
4. Packaging
Injection molds are widely used for producing packaging materials, including bottles, containers, and caps, allowing for efficient mass production.
Innovations in Injection Plastic Molding
As technology evolves, so does the field of injection molding. Here are some of the latest innovations:
1. 3D Printing and Rapid Prototyping
The integration of 3D printing with traditional injection molding processes opens new doors for rapid prototyping, allowing faster and more cost-effective testing of designs.
2. Advanced Materials
Researchers are developing new materials that enhance the performance characteristics of molded parts, including biodegradable plastics and composites that improve strength without increasing weight.
3. Automation and Smart Manufacturing
Incorporating automation in the injection molding process increases efficiency, reduces costs, and leads to higher-quality products through precise control mechanisms.
4. Energy Efficiency
Modern injection molding machines are designed to consume less energy, reducing the overall environmental impact of production and lowering operational costs for manufacturers.
The Role of Metal Fabricators in Injection Plastic Molding
Metal fabricators are vital in the injection molding industry as they create molds and tooling necessary for the process. The collaboration between plastic mold makers and metal fabricators ensures high-quality, durable molds that lead to consistent production results.
Metal Fabrication Techniques Used
- CNC Machining: Precise cutting and shaping of metal used to create intricate mold designs.
- Wire EDM: An advanced method for making detailed and complex molds with high accuracy.
- Blanking and Punching: Techniques to create mold components before assembly.
- Welding: Joining different metal parts to create the structure of the mold.
Quality Control in Injection Molding
Quality assurance is critical in the injection molding process to ensure that every part meets the specified standards.
Methods of Quality Control
- In-Process Monitoring: Continual monitoring of the injection cycle to detect any deviations.
- Dimensional Inspection: Checking the dimensions of molded parts to ensure they meet the specified tolerances.
- Material Testing: Analyzing the physical properties of the materials used to ensure they comply with industry standards.
- Final Product Inspection: Post-production audits of random samples to assess overall quality.
Future Trends in Injection Plastic Mold
The future of injection molding looks promising, with several trends shaping the industry:
1. Sustainability Practices
With growing awareness of environmental issues, manufacturers are focusing on sustainable practices. This includes using recycled materials and energy-efficient processes.
2. Customization and Personalization
As consumer demands shift towards unique products, customized injection molding processes will likely become more prevalent, allowing businesses to meet specific consumer needs.
3. Enhanced Software and Design Tools
The rise of advanced simulation software aids in the mold design process, enabling rapid iterations and optimizations before actual production begins.
4. Collaborative Robots (Cobots)
Integrating cobots into the molding process can enhance production efficiency while ensuring a safe work environment by minimizing human-machine interactions.
Conclusion
In conclusion, the use of injection plastic molds represents a cornerstone of modern manufacturing. As the industry evolves, innovations in technology, materials, and processes will continue to drive efficiency and sustainability, presenting vast opportunities for businesses across various sectors.
For more detailed insights into injection plastic molds and to explore how deepmould.net can assist you in your manufacturing needs, please reach out to us. Together, we can navigate the future of manufacturing innovation.
© 2023 deepmould.net